Series Production
Here is how we streamline and maintain your ideas into long-term and reliable series production.
Your Innovation, Our Facilities
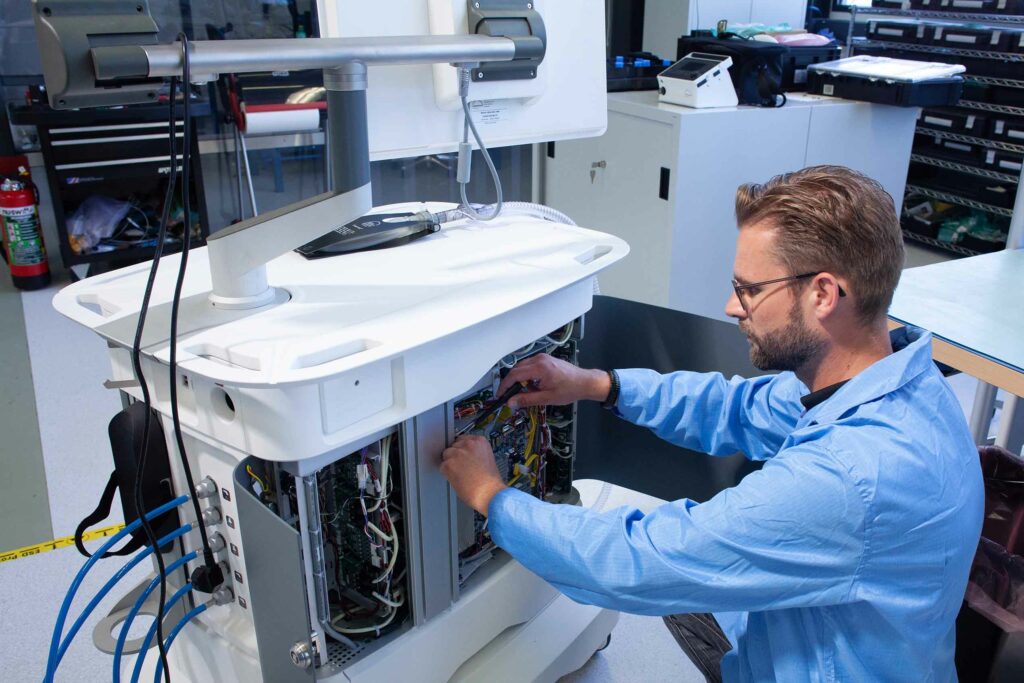
Client Reviews
What our clients say
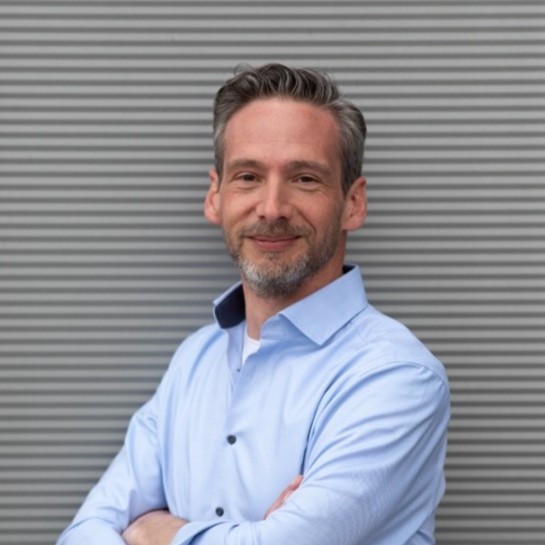
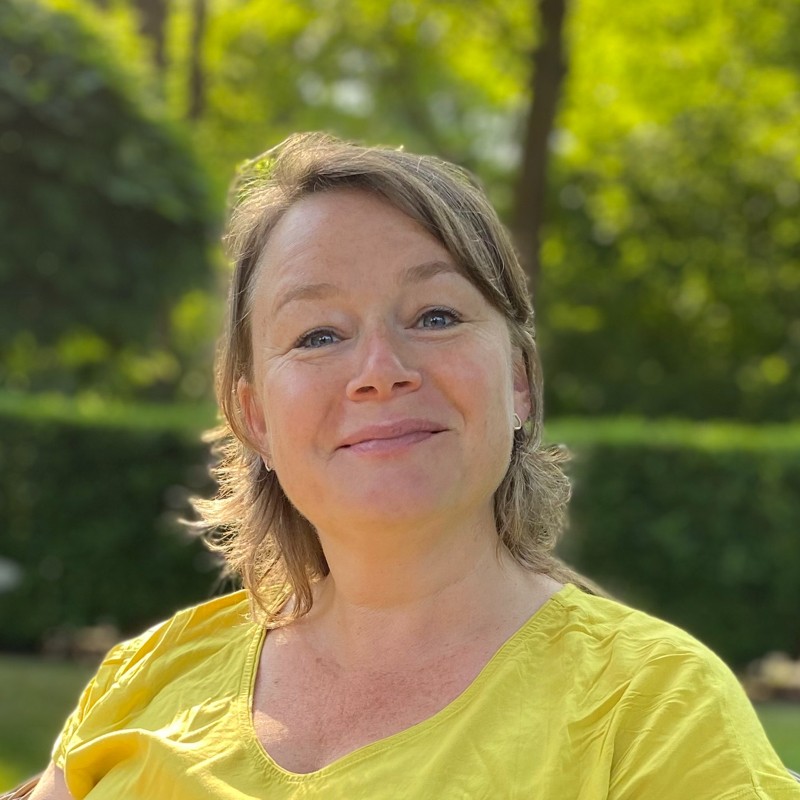
Seven Steps to Series Production
➊
Assessing What You Have
• What production information do you have already?
• How ready is your product for series production?
• What is still missing, and what must be done to start production?
➋
Discussing Your Scope
We discuss the assessment results with you to determine your way forward.
➌
Planning Your Production
Based on our discussion, we will draw up a project and resource planning for the coming steps. If you’ve already compiled your own production documentation, we will review it to see whether we understand your wishes, and how it fits our schedule.
➏
Determining Final Batch Prices
In this step, we finalise the batch production price. This includes costs based on the completed technical details, insights gained from the exploratory assembly phase, and production planning (expected planning and batch sizes).
➎
Exploratory Assembly
With your own staff present, we will set up a preliminary assembly line for production. We then assemble the first device to find out whether there are any issues which we need to take care of first, to ensure a smooth process.
➍
Purchasing Supplies
Our purchasing department will start purchasing the necessary tools and resources to start building your device. Of course, you will be involved in this process.
➐
Series Production
After you agree to our pricing indications, everything is now ready to start producing your product! One of our team members will be appointed as your Technobis product owner. They will be your single point of contact, and are responsible for ensuring a smooth production process, as well as clear communication with you. Periodically, we will also review the production process, to determine wether it needs updating. It may happen that suppliers stop producing certain parts and components. which influences your product. Technobis will help you find a solution.
Full support during product life cycle
- Document Management (ISO standards)
- Maintain production documentation
- Obsolescence management
- Customer specific design
- Cost optimization by
- Value engineering
- Reviewing manufacturability
- functionality improvements
- Assembly improvements
Why Technobis?
The following are a selection of products we help produce and improve:
- Mechatronics
- Precision mechanics
- Electronics
- Commissioning / Factory acceptance test
- Precision mechanics
- Optics
- Software installation
- Commissioning / Factory acceptance test
- Mechatronics
- Precision mechanics
- electronics
- Software installation
- Verification
- Commissioning / Factory acceptance test
- Precision mechanics
- High pressure / high temperature equipment
electronics - Software installation
- Commissioning / Factory acceptance test
- Optics
- Precision mechanics electronics
- Software installation
- Commissioning / Factory acceptance test
- Optics
- Precision mechanics
- electronics
- Software installation
- Commissioning / Factory acceptance test
Long-Term Focus, Close-Knit Cooperation
Technobis strives to be a production partner for the longer term. Benefits for you include that we learn to thoroughly understand your specific requirements, keep a close watch on production quality, periodically review your design, and maintain correct and up-to-date documentation required for your certification.
Our Facilities, Your Advantage
With Technobis as your partner, you have full access to the following state-of-the-art facilities:
- ESD-Compliant assembly & test room
- Conditioned labs for prototyping, and pre-series verification & validation
- Vibration-isolated labs
- Down-flow lab
- Cleanroom (class 8)
Market focus
We help reduce production costs and increase output of medicine by developing and improving pharmaceutical technology.
When you want to make a difference at a molecular level, Technobis helps you develop and improve extreme-precision laboratory equipment.
At Technobis, we combine skill, experience, and state-of-the-art facilities to help you create high-precision medical solutions.
Work together?
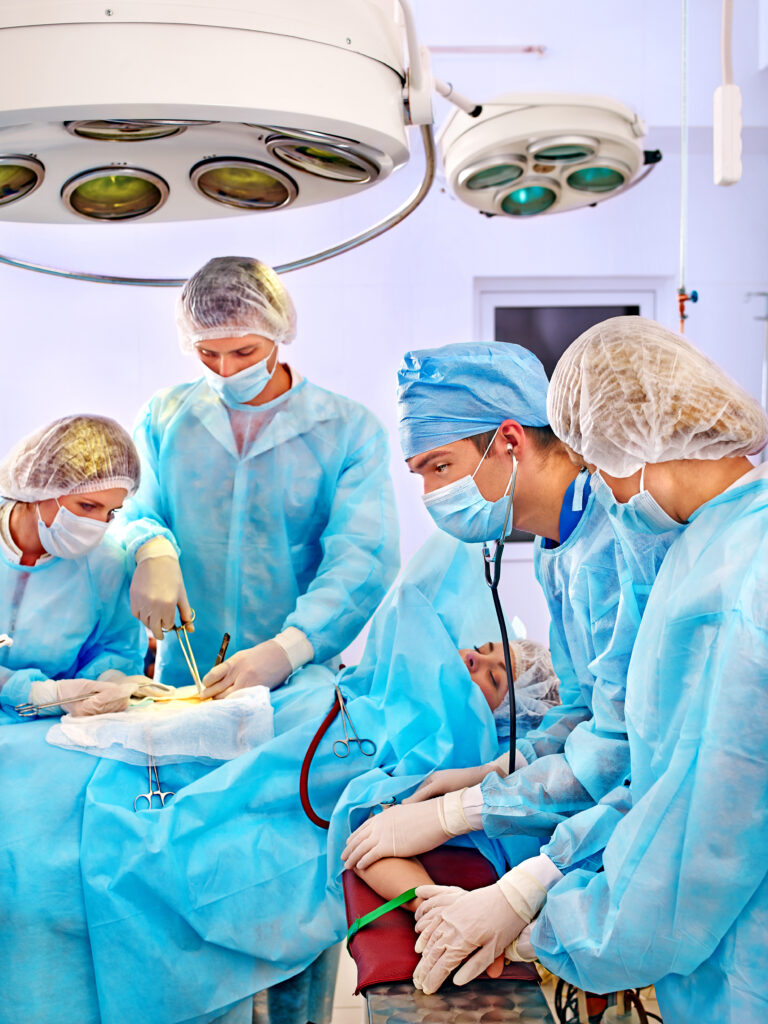
- Skills, tooling & facilities
Skills
- Precision mechanics
- Optics
- Electronics
- Software installation / verification
- Commissioning and Factory
acceptance testing - Mechatronics
Tooling
- Interactive SOLIDWORKS
- Composer Assembly Instructions
- Tracking of assembly quality
- Odoo ERP
- Engage: E-QMS ISO 13485
- Qooling: E-QMS ISO 13485
Facilities
- Assembly & test room, ESD compliant
- Conditioned labs for prototyping and pre-series verification & validation
- Vibration isolated labs
- Down-flow lab
- Cleanroom, class 8
- Proto workshop turning and milling & 3D printing facility